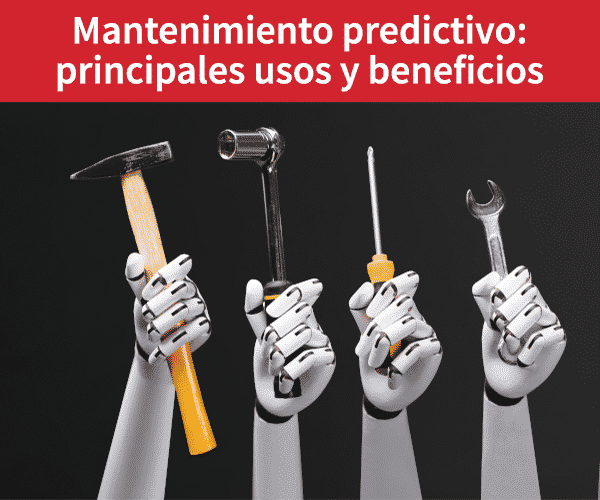
- Mantenimiento
Mantenimiento predictivo: principales usos y beneficios
Para reducir sus costes operativos a la vez que prolonga la vida útil de sus equipos, cada vez más industrias se pasan al mantenimiento predictivo. A continuación, se muestra el panorama general de su uso en aeronáutica, el sector ferroviario, la industria de la automoción y el sector energético. Más vale prevenir que curar. Basándose en este viejo refrán, el mantenimiento predictivo tiene como objetivo vigilar el comportamiento de un equipo en el tiempo y prever las averías antes de que estas se produzcan: es lo que siempre han deseado los profesionales del mantenimiento. El mantenimiento predictivo sustituye y mejora los modelos de mantenimiento existentes, que han mostrado sus propias limitaciones. Con el mantenimiento correctivo, hay que esperar a que se produzca un fallo antes de intervenir. Con el mantenimiento preventivo, los periodos de mantenimiento están predeterminados en función de índices estadísticos de desgaste, mientras que el equipo tal vez habría podido funcionar durante muchos meses.
El dúo perfecto: IA + IoT
Asociando la inteligencia artificial con el Internet de las cosas (IoT), el mantenimiento predictivo compara el flujo de datos cargados en tiempo real por los dispositivos conectados con el historial de uso de la máquina, para poder identificar las señales de advertencia de una avería y, a continuación, iniciar los procedimientos de manera proactiva. Desde finales del año 2010, el mantenimiento predictivo está ganando terreno debido a diversos factores: por un lado, por supuesto, los recientes progresos en materia de machine learning y deep learning; y por otro lado, la reducción del coste de los objetos conectados, que permite dotar a los equipos de un mayor número de sensores, a modo de una auténtica estrategia de IoT industrial.
Productividad optimizada en actividades de mantenimiento
No solo las tecnologías disponen ya de un buen grado de madurez, sino que ya se puede medir el retorno de la inversión sobre los primeros proyectos de mantenimiento predictivo. Las empresas pioneras prolongan la vida útil de sus equipos a la vez que reducen los periodos de inactividad. Los fabricantes optimizan, además, la gestión de su stock de piezas de repuesto, sustituyendo únicamente las que son necesarias. Desde el punto de vista de la gestión de equipos, se inmoviliza en el momento adecuado y en el lugar correcto al técnico de mantenimiento más competente para un problema dado.
Aeronáutica: el jugoso mercado MRO
La industria aeronáutica es una de las primeras en utilizar el mantenimiento predictivo. Después del combustible, el mantenimiento representa, de hecho, su mayor partida de gasto. Con el crecimiento exponencial del tráfico aéreo, las compañías aéreas también tratan de minimizar el tiempo durante el cual sus aeronaves están inmovilizadas en tierra. Este mercado, designado MRO (maintenance, repair and overhaul – mantenimiento, reparación y operaciones) presenta un futuro prometedor. Debería pasar de 75.600 millones de dólares en 2017 a 109.000 millones de dólares en 2027, según las previsiones a nivel mundial de la consultora estadounidense Oliver Wyman. Es, sin duda, un mercado jugoso en el que se han fijado todos los participantes de la cadena: compañías aéreas, fabricantes de aviones y fabricantes de motores. Air France KLM comercializa su propia solución de mantenimiento predictivo (Prognos). El grupo Airbus lanzó, en 2017, la plataforma Skywise en la que recoge datos de miles de aviones en vuelo para mejorar su uso, incluidos los de EasyJet. Gracias a los sensores con los que cuentan los motores de sus helicópteros, el fabricante de componentes Safran hace un seguimiento continuo de su estado (potencia, temperatura, presión, etc.). Los gigantes de la era digital – Google, Microsoft, IBM, Amazon Web Services, etc. – también ofrecen soluciones específicas.
Sector ferroviario: optimizar y proteger una red en proceso de envejecimiento
Otro medio de transporte, otros retos. La industria ferroviaria también presta mucha atención al mantenimiento predictivo. Para darse cuenta de ello, basta con recordar las múltiples averías que sufrió recientemente la estación de tren de Montparnasse, desde el incendio de un transformador hasta el corte del suministro eléctrico. De hecho, hace ya varios años que la empresa pública francesa de ferrocarriles, SNCF, está desarrollando un plan muy ambicioso de IoT industrial. En 2016, la compañía ferroviaria anunciaba una inversión de nada menos que 500 millones de euros para optimizar la seguridad de su red.
Drones para inspeccionar las vías
Para empezar, mediante la vigilancia de los 30.000 km de líneas ferroviarias. Unos sensores permiten prevenir fenómenos como la dilatación y la deformación de las vías. Las agujas y los pasos a nivel también son objeto de una inspección en profundidad, así como los alrededores de las vías. La empresa SNCF utiliza drones para localizar posibles obstáculos, en especial la vegetación circundante que podría invadir los carriles. A nivel de las infraestructuras, la supervisión automática de los pantógrafos – los brazos mecánicos articulados colocados en el techo del tren, que suministran corriente eléctrica – permite prevenir las famosas roturas de catenaria. El material rodante, a su vez, está cada vez más conectado para evitar fallos de climatización, tan perjudiciales en épocas de calor intenso. Pueden instalarse sensores en las puertas correderas de los trenes o en los asientos de los viajeros para acelerar su sustitución. Por último, la empresa SNCF optimiza el uso de estas estaciones, poniendo sensores en los ascensores, las escaleras mecánicas o las luminarias.
Automoción: ¿están los fabricantes en vías de ser “uberizados”?
Pasemos del transporte público a los desplazamientos individuales en automóvil. El sector de la automoción no ha alcanzado el mismo nivel de madurez en este tema. El mantenimiento sigue estando vinculado al ciclo clásico de revisiones del vehículo. Además de una revisión cada 30.000 km, el concesionario recomendará, por ejemplo, cambiar la correa de distribución cada cinco años o a los 120.000 kilómetros. El número cada vez mayor de vehículos conectados, sin embargo, puede servir para que los fabricantes aprovechen el gran volumen de datos con los que cuentan para proponer prestaciones de diagnóstico a distancia. En el ámbito empresarial, los gestores de flotas también piden aprovechar estos datos para amortizar mejor sus vehículos. Esta batalla por los datos es fundamental, puesto que los fabricantes pueden sufrir una desintermediación. Con sus sistemas operativos integrados CarPlay y Android Auto, Apple y Google ya se han subido a bordo. Startups como Drust y Carfit proponen, por su parte, instalar una carcasa que, una vez conectada a la toma de diagnóstico OBD o a partir de análisis vibratorios del vehículo, podrá prever los fallos.
Sector energético: supervisión en tiempo real de las infraestructuras
Con la llegada de contadores inteligentes como Linky y Gazpar, los gestores de redes de distribución de energía (electricidad, gas y agua) han entrado de lleno en el mundo de los datos. Se aplica el mantenimiento predictivo para reducir las visitas físicas en sus infraestructuras. Suez propone una solución informática (Aquadvanced) para controlar las redes de agua potable en tiempo real, recordando que el “90% de las fugas son invisibles”. Como fabricante de válvulas de alto rendimiento para el sector nuclear y el energético, Daher ha instalado sensores en sus instalaciones para analizar las señales más débiles (vibraciones, temperatura, caudal, etc.) y prever los posibles fallos. En el ámbito de las energías renovables, Engie ha invertido 12 millones de euros en su plataforma digital Darwin, que pretende analizar las 24 horas del día, los 7 días de la semana, los datos transmitidos por los sensores instalados en su parque eólico y solar (velocidad de rotación de las aspas de los aerogeneradores, temperatura de los paneles fotovoltaicos, etc.). Según Les Echos, permitirá al proveedor energético “ganar en cinco años 24 millones de euros sobre los costes operativos y de mantenimiento“. Un ROI muy rápido.
Artículos relacionados
-
- Mantenimiento
- Productividad
7 prácticas para optimizar la gestión de sus órdenes de trabajo de mantenimiento
28 de junio de 2018 -
- Mantenimiento
- kpis
MTBF vs MTTR: su valor en los Servicios de Campo
10 de febrero de 2023